切向高温导热油流量计小流量测量响应特性
点击次数:2105 发布时间:2021-01-19 14:37:52
摘要:应用动量定理研究高温导热油流量计的基本工作机理及仪表系数模型。通过数值仿真和流动实验,分析切向高温导热油流量计叶片未转动及转动时流体在高温导热油流量计的分布情况,阐述切向涡轮计叶片转动机理。基于小流量实验装置,考察了高温导热油流量计在单相水及单相油条件下的响应特性。高温导热油流量计在纯水与纯油介质中,启动排量分别为0.081m3/d与0.08m3/d,均远远低于普通螺旋式高温导热油流量计的0.5m3/d,证明高温导热油流量计在低流量测量中具有良好的应用前景。
引言:
高温导热油流量计广泛应用于小流量测量中。与轴向式涡轮流量传感器相比,切向涡轮流量传感器的启动排量更低,测量灵敏度更高,动态响应速度更快。随着国内大部分油田进入开发中后期,低产井数量逐年增多,大量油井的日产量低于5m3/d,单层产量甚至低于1m3/d。低产液井对测井仪器提出了新的要求,传统螺旋式高温导热油流量计对低流量的响应较差,启动排量较高,难以对低产井的井下流动进行有效监测。为此,提出采用高温导热油流量计测量小流量。本文通过理论推导、数值仿真及小流量流动装置实验,对高温导热油流量计测量机理和响应特性进行了研究。
1 高温导热油流量计工作原理:
高温导热油流量计基本构造见图1。被测流体在流经叶轮之前流道会减缩,流速增加,流体经过叶轮后叶片旋转,磁电传感器记录叶片转动频率,得到被测流体相对应的流量。
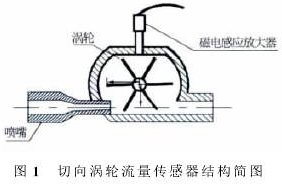
涡轮在转动时所受的力矩大致可分:流体对涡轮的推动力矩Tr,机械摩擦力矩Trm,流体对涡轮产生的流动阻力矩Trf和电磁阻力矩Tre。涡轮运动方程可以表示为

式中,J为涡轮转动惯量;ω为涡轮转动角速度。涡轮正常工作时,ω可近似看作定值(切向涡轮转动时由于驱动力矩随着位置变化而变化,所以转动角速度ω也是变化的,这里将ω看作定值)。
如图2所示,高温导热油流量计流道收缩后面积为A,从流道流出的流体速度为v1,从涡轮流出的流体速度为v2;v1和v2与涡轮叶片速度方向的夹角为α1和α2,涡轮的转动角速度为ω,假设出口处流体相对运动速度的方向平行于叶片方向。
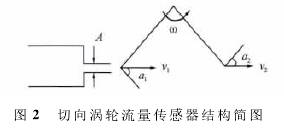
在涡轮转动时,只有垂直叶片方向的力对驱动力矩有贡献,因此只考虑垂直叶片方向的驱动力f。
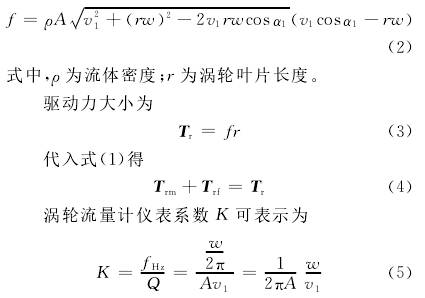
式中,fHz为转动频率;Q为流量。
2 高温导热油流量计流场分布特性仿真分析:
Workbench是ANSYS公司开发的协同仿真环境,大大简化了仿真过程中各模块间的交互操作。通过几何建模、网格划分、计算求解、后处理等过程,可以比较准确地仿真复杂机械模型的各个物理参数的场分布。
根据实际情况采用了二维计算,并将计算域划分为2个部分:叶轮转动部分和入口出口部分(见图3)。
在图3中叶轮部分和入口出口部分均采用四边形网格,网格数各约2万,整个计算域网格数为4万。入口出口部分为静止网格采用参考系,叶轮部分为动网格,绕圆心转动,同时采用相对参考系,参考系转动速度与网格转速相同。
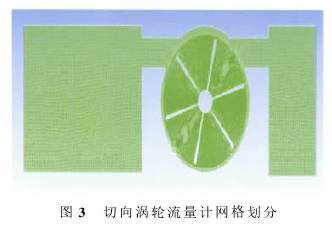
高温导热油流量计仿真模型见图4。图4中右侧入口和左侧出口均宽20mm,在计算中分别设置为速度入口和速度出口,转动部分直径(图4中D1)为18mm,叶片顶端半径为8.5mm,转动腔上半部分直径(D3)为20mm,转动腔下半部分直径(D2)为19mm,转动腔入口出口宽度均为4mm。
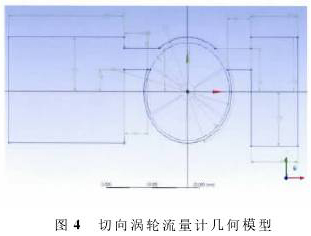
图5、图6中速度入口分别为0.08m3/d及1m3/d。如图5所示,当流速较低时,流体在切向涡轮内可以近似看成绕角流动,此时腔体内叶片压强对称分布,基本上不产生压差,无法驱动涡轮叶片转动;随着流速增大,流体在流入靠近入口的腔体时,在腔体内产生旋涡,旋涡的运动导致叶片壁面压强分布不均匀,从而产生驱动矩,如图6所示。可以看出对驱动力矩有贡献的是靠近入口的腔体,其他腔体基本上不产生压差。
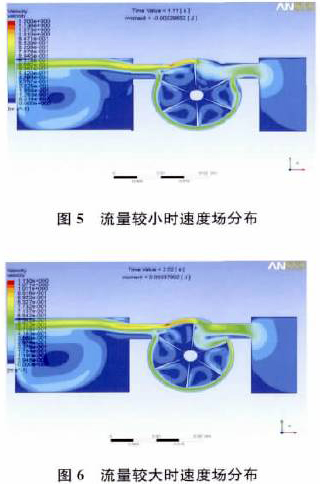
为了验证仿真的准确性,通过室内实验对其验证。切向涡轮采用可视化研究平台,整个涡轮的结构都采用亚克力板雕刻组装而成。如图7所示,水箱主要提供稳定水压,水平切向涡轮做成开口系统并放置在实验支撑架上,前置阀门可控制水流,在需要更换切向涡轮的零件时可关闭,控制阀门主要是控制流经切向涡轮的流量,流量测量仍采用传统可靠的容积时间法。实验时以染色剂作为示踪剂,以观察流场的分布情况。
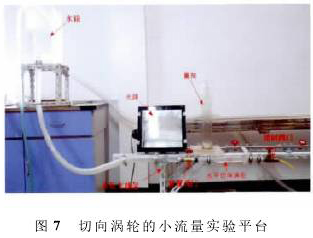
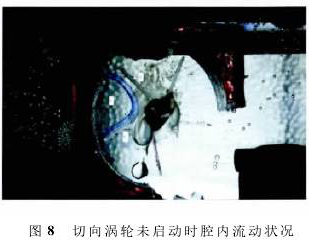
如图8所示,记录的是未启动时切向涡轮内的流场,水从图8左侧流入涡轮,从右侧流出,实验时水的流速很低(0.05m3/d),腔体1中的流动可近似看作不可压缩无旋绕角流动,此时流体在腔体1中的速度可看成对称分布,由伯努利方程算得的压强也是对称分布,此时2个壁面几乎没有压强差,所以涡轮未启动。
图9记录的是切向涡轮正常转动时的流场,图9中水从左向右流动,实验时水速较快(1m3/d),涡轮叶片顺时针转动。水速变大后,扰动变大,不再是无旋绕角流动,腔体1中流体形成一个运动的旋涡,导致腔内压强分布不再对称,产生压差,致使涡轮叶片转动,旋涡在随叶片运动到腔体2中时逐渐耗散消失。数值仿真的计算结果与物理实验的结果基本一致。
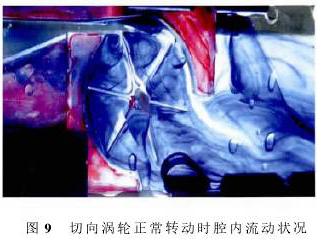
3 切向涡轮在单相流体中响应特性:
为了验证切向涡轮在单相流体中的响应情况,在全集流条件下对其在单相水及单相油介质中响应规律进行了研究。对于单相水的涡轮响应情况,进行了在0~6m3/d流速范围内的涡轮响应实验,测得单相水介质中涡轮的启动排量为0.081m3/d,涡轮响应情况见图10。经过拟合后的响应关系为ω=6.49Q-1.446。
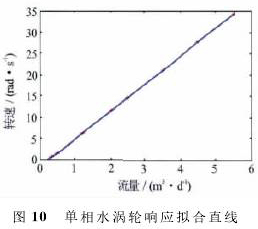
采用同样的方法,对单相油条件下涡轮响应规律进行研究(见图11),测得单相油的启动排量为0.08m3/d。对单相油的实验结果进行拟合,可得单相油的响应曲线为ω=6.73Q-6.72。与水对比而言,油的拟合曲线斜率更大,即随着流量增加转速增加得略快。
为了深入分析高温导热油流量计在单相低流量条件下的响应特点,将流量作为横坐标,仪表K值即转速/流量作为纵坐标,绘制单相水(见图12)和单相油(见图13)的高温导热油流量计特性曲线。
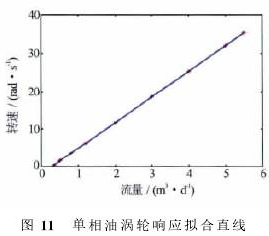
为了深入分析切向高温导热油流量计在单相低流量条件下的响应特点,将流量作为横坐标,仪表K值即转速/流量作为纵坐标,绘制单相水(见图12)和单相油(见图13)的切向高温导热油流量计特性曲线。
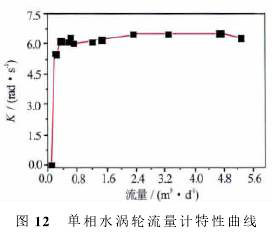
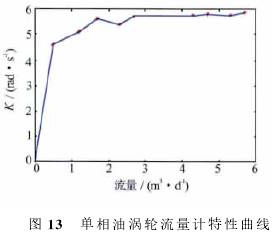
可以看出,涡轮启动后*先进入一个非线性段,在非线性相应段,K值随着流量增加而增大;当流量比较大(单相水超过0.5m3/d,单相油超过1m3/d)时,涡轮进入线性段,在线性响应段,K值达到峰值,有相对较小的波动。
4 结论:
(1)数值仿真结果与物理实验结果基本一致,当流速低于启动排量,涡轮未启动时,流体沿叶片做绕角运动,叶片两侧压力相等,叶片不转动;当流速高于启动排量,涡轮转动时,流体在腔内产生旋涡,造成叶片两边压差,从而造成叶片转动。
(2)高温导热油流量计在纯水与纯油介质中,启动排量分别为0.081m3/d与0.08m3/d,均远远低于普通螺旋式高温导热油流量计0.5m3/d的启动排量,在低流量测量具有良好的前景。
(3)高温导热油流量计在未达到稳定转动前,K值不断增大,稳定转动后 K值趋于一条直线,具有良好的线性关系。
引言:
高温导热油流量计广泛应用于小流量测量中。与轴向式涡轮流量传感器相比,切向涡轮流量传感器的启动排量更低,测量灵敏度更高,动态响应速度更快。随着国内大部分油田进入开发中后期,低产井数量逐年增多,大量油井的日产量低于5m3/d,单层产量甚至低于1m3/d。低产液井对测井仪器提出了新的要求,传统螺旋式高温导热油流量计对低流量的响应较差,启动排量较高,难以对低产井的井下流动进行有效监测。为此,提出采用高温导热油流量计测量小流量。本文通过理论推导、数值仿真及小流量流动装置实验,对高温导热油流量计测量机理和响应特性进行了研究。
1 高温导热油流量计工作原理:
高温导热油流量计基本构造见图1。被测流体在流经叶轮之前流道会减缩,流速增加,流体经过叶轮后叶片旋转,磁电传感器记录叶片转动频率,得到被测流体相对应的流量。
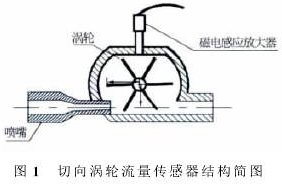
涡轮在转动时所受的力矩大致可分:流体对涡轮的推动力矩Tr,机械摩擦力矩Trm,流体对涡轮产生的流动阻力矩Trf和电磁阻力矩Tre。涡轮运动方程可以表示为

式中,J为涡轮转动惯量;ω为涡轮转动角速度。涡轮正常工作时,ω可近似看作定值(切向涡轮转动时由于驱动力矩随着位置变化而变化,所以转动角速度ω也是变化的,这里将ω看作定值)。
如图2所示,高温导热油流量计流道收缩后面积为A,从流道流出的流体速度为v1,从涡轮流出的流体速度为v2;v1和v2与涡轮叶片速度方向的夹角为α1和α2,涡轮的转动角速度为ω,假设出口处流体相对运动速度的方向平行于叶片方向。
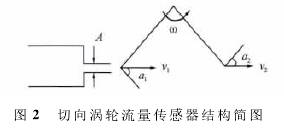
在涡轮转动时,只有垂直叶片方向的力对驱动力矩有贡献,因此只考虑垂直叶片方向的驱动力f。
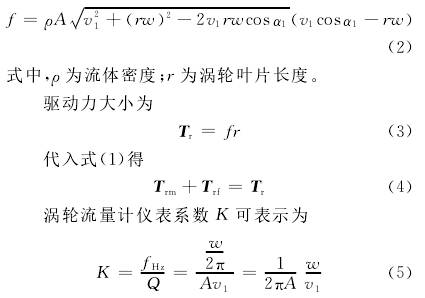
式中,fHz为转动频率;Q为流量。
2 高温导热油流量计流场分布特性仿真分析:
Workbench是ANSYS公司开发的协同仿真环境,大大简化了仿真过程中各模块间的交互操作。通过几何建模、网格划分、计算求解、后处理等过程,可以比较准确地仿真复杂机械模型的各个物理参数的场分布。
根据实际情况采用了二维计算,并将计算域划分为2个部分:叶轮转动部分和入口出口部分(见图3)。
在图3中叶轮部分和入口出口部分均采用四边形网格,网格数各约2万,整个计算域网格数为4万。入口出口部分为静止网格采用参考系,叶轮部分为动网格,绕圆心转动,同时采用相对参考系,参考系转动速度与网格转速相同。
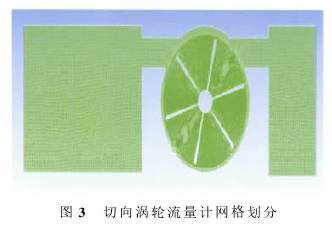
高温导热油流量计仿真模型见图4。图4中右侧入口和左侧出口均宽20mm,在计算中分别设置为速度入口和速度出口,转动部分直径(图4中D1)为18mm,叶片顶端半径为8.5mm,转动腔上半部分直径(D3)为20mm,转动腔下半部分直径(D2)为19mm,转动腔入口出口宽度均为4mm。
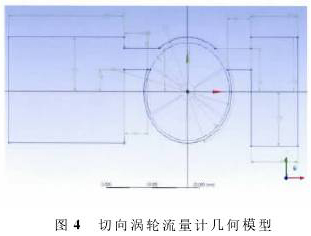
图5、图6中速度入口分别为0.08m3/d及1m3/d。如图5所示,当流速较低时,流体在切向涡轮内可以近似看成绕角流动,此时腔体内叶片压强对称分布,基本上不产生压差,无法驱动涡轮叶片转动;随着流速增大,流体在流入靠近入口的腔体时,在腔体内产生旋涡,旋涡的运动导致叶片壁面压强分布不均匀,从而产生驱动矩,如图6所示。可以看出对驱动力矩有贡献的是靠近入口的腔体,其他腔体基本上不产生压差。
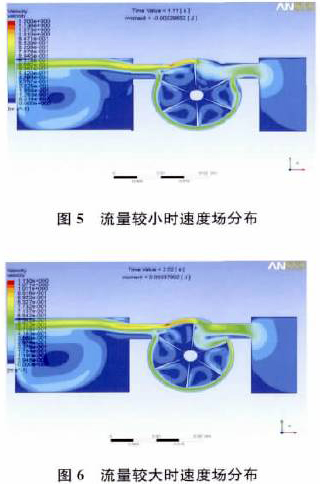
为了验证仿真的准确性,通过室内实验对其验证。切向涡轮采用可视化研究平台,整个涡轮的结构都采用亚克力板雕刻组装而成。如图7所示,水箱主要提供稳定水压,水平切向涡轮做成开口系统并放置在实验支撑架上,前置阀门可控制水流,在需要更换切向涡轮的零件时可关闭,控制阀门主要是控制流经切向涡轮的流量,流量测量仍采用传统可靠的容积时间法。实验时以染色剂作为示踪剂,以观察流场的分布情况。
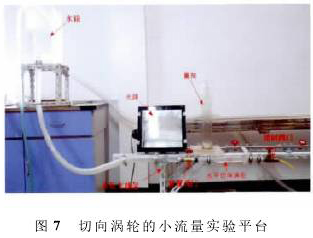
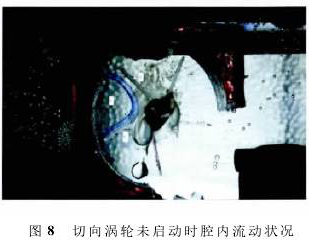
如图8所示,记录的是未启动时切向涡轮内的流场,水从图8左侧流入涡轮,从右侧流出,实验时水的流速很低(0.05m3/d),腔体1中的流动可近似看作不可压缩无旋绕角流动,此时流体在腔体1中的速度可看成对称分布,由伯努利方程算得的压强也是对称分布,此时2个壁面几乎没有压强差,所以涡轮未启动。
图9记录的是切向涡轮正常转动时的流场,图9中水从左向右流动,实验时水速较快(1m3/d),涡轮叶片顺时针转动。水速变大后,扰动变大,不再是无旋绕角流动,腔体1中流体形成一个运动的旋涡,导致腔内压强分布不再对称,产生压差,致使涡轮叶片转动,旋涡在随叶片运动到腔体2中时逐渐耗散消失。数值仿真的计算结果与物理实验的结果基本一致。
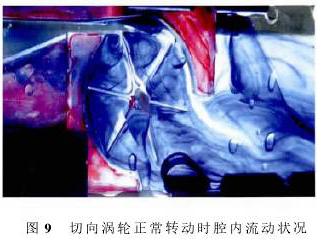
3 切向涡轮在单相流体中响应特性:
为了验证切向涡轮在单相流体中的响应情况,在全集流条件下对其在单相水及单相油介质中响应规律进行了研究。对于单相水的涡轮响应情况,进行了在0~6m3/d流速范围内的涡轮响应实验,测得单相水介质中涡轮的启动排量为0.081m3/d,涡轮响应情况见图10。经过拟合后的响应关系为ω=6.49Q-1.446。
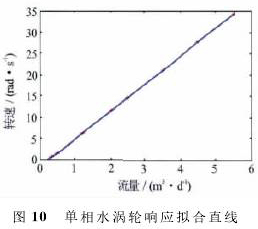
采用同样的方法,对单相油条件下涡轮响应规律进行研究(见图11),测得单相油的启动排量为0.08m3/d。对单相油的实验结果进行拟合,可得单相油的响应曲线为ω=6.73Q-6.72。与水对比而言,油的拟合曲线斜率更大,即随着流量增加转速增加得略快。
为了深入分析高温导热油流量计在单相低流量条件下的响应特点,将流量作为横坐标,仪表K值即转速/流量作为纵坐标,绘制单相水(见图12)和单相油(见图13)的高温导热油流量计特性曲线。
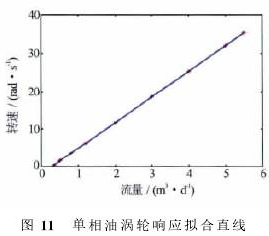
为了深入分析切向高温导热油流量计在单相低流量条件下的响应特点,将流量作为横坐标,仪表K值即转速/流量作为纵坐标,绘制单相水(见图12)和单相油(见图13)的切向高温导热油流量计特性曲线。
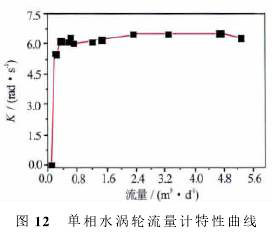
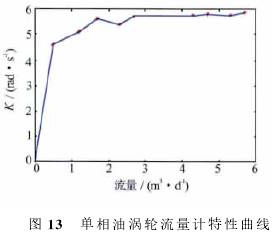
可以看出,涡轮启动后*先进入一个非线性段,在非线性相应段,K值随着流量增加而增大;当流量比较大(单相水超过0.5m3/d,单相油超过1m3/d)时,涡轮进入线性段,在线性响应段,K值达到峰值,有相对较小的波动。
4 结论:
(1)数值仿真结果与物理实验结果基本一致,当流速低于启动排量,涡轮未启动时,流体沿叶片做绕角运动,叶片两侧压力相等,叶片不转动;当流速高于启动排量,涡轮转动时,流体在腔内产生旋涡,造成叶片两边压差,从而造成叶片转动。
(2)高温导热油流量计在纯水与纯油介质中,启动排量分别为0.081m3/d与0.08m3/d,均远远低于普通螺旋式高温导热油流量计0.5m3/d的启动排量,在低流量测量具有良好的前景。
(3)高温导热油流量计在未达到稳定转动前,K值不断增大,稳定转动后 K值趋于一条直线,具有良好的线性关系。