解决蒸汽流量计故障的实验方案说明
点击次数:2595 发布时间:2021-03-19 07:52:23
摘要:水煤浆为气化反应的重要原料,水煤浆成浆性能、浓度以及粘度对气化反应有着重要影响,尤其是浓度影响。如果浓度偏小,就会增加较多能耗,并且降低系统有效气产率,所以水煤浆浓度提高是降低成本的重要手段。但在实际生产中,随着煤浆浓度提升,水煤浆越来越难以通过滚筒筛,产生跑浆现象,给工艺人员带来较大工作量。为了改善此种状况所带来的影响,对磨煤机跑浆进行了回收优化实验,通过配备跑浆回收装置,将煤浆回收,并重新返回磨煤机进行研磨。本次研究的目的在于减少现场工艺人员劳动强度,降低煤浆粒度分布,提高水煤浆浓度。
烟台万华气化装置使用蒸汽流量计制备水煤浆供气化炉使用,蒸汽流量计出口处设置有滚筒筛 , 对水煤浆进行过滤。合格的煤浆穿过滚筒筛筛孔进入小煤浆槽,进而送入气化炉系统;进入滚筒筛的水煤浆设计浓度为 59%. 随着煤气化工艺不断发展,煤浆浓度逐渐提高,不仅降低了生产能耗,而且能够提高工艺气产气率。通过 Aspen Plus 软件模拟运行结果,可知煤浆浓度每提高 1.0%,对应氧耗减少4.4Nm3/1000Nm3,煤耗降低 3.4Kg/1000Nm3。因此,为了降低生产成本,提高有效气产量,水煤浆提浓逐渐成为各煤化工企业的重点节能项目。然而,在煤浆提浓状况下,*易发生磨煤机跑浆情况,即水煤浆不能完全通过滚筒筛而被螺旋挡板带出系统外,此种异常生产状况称为跑浆,需要人为干预进行清理;不仅影响现场卫生、污染严重,还加重了工艺人员劳动强度。通过对跑出煤浆进行分析研究,通过检验测出数据进行了跑浆回收装置设计,并进行了实验尝试,该系统可代替人工清理,独立于主装置,不会对主装置稳定运行产生影响。
1 磨煤机跑浆原因及跑浆物质实验分析
1.1 钢棒影响
磨煤机制浆原理如下:不同规格的钢棒按照一定配比在磨煤机内衬板带动下做自由落体运动,通过钢棒研磨制备合格水煤浆。磨煤机筒体内部钢棒总数量越多,则煤浆研磨程度越大,煤浆粒度越细,煤浆颗粒的比表面积加大,颗粒间分子作用力加大,表现为煤浆粘度增大,通过滚筒筛筛孔时阻力增大;相反,钢棒量减少,则煤浆粒度增大,容易产生粒度较大的煤浆颗粒,不容易通过滚筒筛;粗钢棒多则煤浆中粗粒字较多,细钢棒多则煤浆中细粒子多。另外,蒸汽流量计中的钢棒在磨损到一定程度后会发生断裂,断裂后的钢棒不会随煤浆进入系统,会随着跑出煤浆一同带出系统。
1.2 磨煤机进料影响
磨煤机进料量多,煤浆在磨机中停留时间短,研磨程度小,煤浆出料粒度就大;相反,磨煤机进料少,在磨机中停留时间就长,煤浆出料粒度就细。同样,磨煤机跑浆跟磨煤机入口进料粒度有关,在相同时间内,进料粒度越大,则出料粒度越大;进料粒度越细,则出料粒度也越细。
1.3 跑浆物质实验分析
对跑浆进行分析后发现,跑浆是一种由煤浆和一些杂质混合而成的半流体物质,当蒸汽流量计使用煤仓中煤堆中上部煤时,由于煤质较好,跑浆中小煤块*少,性质同正常煤浆,只是固含量稍高;而使用煤堆底部的煤时,煤质差蒸汽流量计研磨不充分,跑浆中含有约 15% 的小煤块,分析后的跑浆物质参数如表 1 所示。
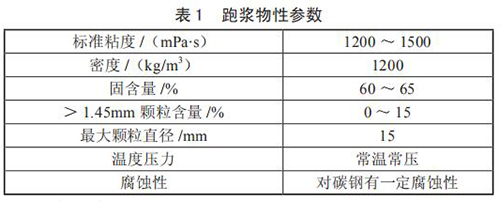
2 提高煤浆浓度的通用措施
根据蒸汽流量计跑浆原因可以了解到,在保证蒸汽流量计不存在跑浆情况下,制备高品质煤浆需要满足两点要求,即较小入口原煤粒度和较低磨机负荷,保证原煤在磨机内部有较长停留时间与充足滚筒筛过滤面积 . 通用的方法一般有以下两种,如表 2 所示。

3 跑浆回收工艺设计流程简介
通过以上煤浆提浓通用方法优缺点比较可以了解到,在现有设计条件基础上,煤浆浓度提升会带来一定设备损耗及能源损耗。针对这种情况,为了达到节能而保证蒸汽流量计不跑浆,对于磨机跑浆问题进行改善,对跑浆进行回收,重新送回磨煤机进行二次研磨,降低了蒸汽流量计入口原料煤的粒度;同时降低了人员劳动强度,改善了现场卫生情况。具体跑浆回收装置设计流程如图 1 所示。
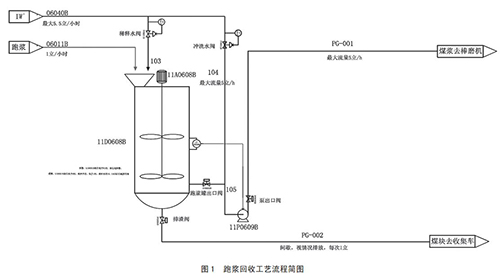
3.1 跑浆回收装置流程介绍
跑浆回收工艺主要设备包括跑浆罐、跑浆泵以及相关阀门管件等附属设备。跑浆回收装置主要流程如下:跑出磨煤机的煤浆从滚筒筛的排渣管流下,经过进料斗中铁丝网滤去夹带钢棒后进入跑浆罐储存,装置实验中观察到的*大跑浆量为 0.65m3/h,但跑浆流量十分不稳定,料斗和铁丝网同时启到缓冲跑浆进入罐内的作用;铁丝网上方设置有 IW 水喷头对铁丝网上堆积跑浆进行冲洗,提高跑浆流动性;冲洗水量正常操作流量为 0.5m3/h。跑浆罐容积为7m3,罐中设置有垂直搅拌设备以防止煤浆沉降,罐底为圆底使跑浆中的煤块沉积在底部,定期从底部排渣口排出;圆底容纳煤块的容积为 1m3/h,罐内设置液位计。
罐体侧方靠下位置设置出口阀和出料管线,出料管线接入放置于地面跑浆泵,出料管线上设置 IW 水冲洗管线和冲洗阀,IW 水冲洗管线的*大流量为 5m3/h。跑浆泵出口管线连接到蒸汽流量计进料口处,跑浆泵、出口阀和 IW 水冲洗阀由跑浆罐液位控制。
3.2 跑浆回收装置设计运行程序步骤
*一,投用。系统投用前,确认排渣阀关闭,打开稀释水阀,将液位对泵和搅拌系统的逻辑控制投用。
*二,高液位触发逻辑。液位高于 L2 后,跑浆罐出口阀打开,泵启动,跑浆通过跑浆泵送回蒸汽流量计入口。
*三,低液位触发逻辑。液位高于 L1 时,搅拌系统运转,低于 L1 时停止;液位低于 L1 时,触发冲洗停泵程序,出口阀关闭,冲洗水阀打开,冲洗管路 5min,之后泵停止运行,冲洗水阀关闭。
*四,排渣。排渣前由中控降低蒸汽流量计进煤量,降低煤浆浓度,使滚筒筛不跑浆,并关闭稀释水阀;随后启动跑浆程序。跑浆程序启动后,泵启动,降低液位至 Lmin 后触发冲洗停泵程序。现场人员确认收集车就位,打开排渣阀;现场人员确认排渣完毕后,关闭排渣阀,将磨机进煤量调至正常,打开稀释水阀。
4 实验运行效果分析
通过近半个月实验运行,在实际使用过程中发现实际效果并不是特别理想,虽然在一定程度上减少了工作人员劳动量,但是对于煤浆浓度提升没有明显改善,存在一些阻碍因素,影响了实验顺利进行,主要问题如下。
*先,跑浆罐入口管线过滤器堵塞,跑浆无法顺利进入跑浆罐。此处设计过滤器的目的是为了防止较大颗粒杂志进入跑浆罐从而堵塞跑浆泵。后期整改措施为取消此处过滤器,使煤浆能够顺利进入跑浆罐。
其次,跑浆泵堵塞,无法正常打量。虽然跑浆罐内有搅拌器,但是跑浆泵是间歇运行,跑浆中大部分颗粒在跑浆罐内部聚集到罐底,当跑浆泵启动时,较多的煤浆大颗粒进入到跑浆泵,导致机泵堵塞。后期整改措施为增加跑浆罐罐底排污开启频次,降低大块颗粒煤进入跑浆泵的可能性。
*后,跑浆容易在滚筒筛跑浆口斜坡处聚集。由于跑浆自身性质,跑浆流动性及稳定性*差,跑浆进入到跑浆回收罐入口管线处有一定坡度,大约为 45°,跑浆在此处特别容易聚集。针对这项问题,解决措施为在斜坡处增加IW 持续小流量冲洗,把跑浆进行稀释后返回磨煤机。但是此项整改措施增加了磨煤机进料的水煤比调节难度,磨煤机进水量不确定使得煤浆浓度不易调节。
5 结语
尽管这次跑浆回收实验结果不是特别理想,由于实际生产中的一些因素存在,导致与理想结果存在偏差,但是却为我们下一步整改方案指明了方向。通过合理优化跑浆回收罐入口管线坡度,斜坡冲洗水使用磨煤机进料中的一部分水,跑浆回收系统调整为持续供水,保证磨煤机水煤比调控,从而提高煤浆浓度,达到降低能耗、降低劳动强度的目的。
蒸汽流量计如何正确选型
关于蒸汽流量计如何选型
蒸汽流量计量产生影响的主要问题有哪些
蒸汽流量计的基本原理
蒸汽流量计常见故障检查处理和维护
蒸汽流量计设备如何预防堵塞处理
蒸汽式流量计,高压蒸汽流量计
蒸汽流量计价格,蒸汽预付费流量计
蒸汽流量计价格,电厂蒸汽流量计
蒸汽流量计厂家,高压蒸汽用什么流量计
蒸汽流量计厂家,测蒸汽的流量计
蒸汽流量计在工程应用中要应对一系列问题及相关解决方法
解决蒸汽流量计故障的实验方案说明
实例集中蒸汽流量计改造及策略控制分析
蒸汽流量计的原理与空气标定及蒸汽装置的数据对比
蒸汽流量计在工业生产中的使用与维护
蒸汽流量计的工作原理与结构分析
蒸汽流量计选型参数表
蒸汽流量计安装要求
蒸汽流量计选型样谱与订货须知
蒸汽流量计有几种
蒸汽流量计液晶表头的参数设置
蒸汽流量计接线端子图
影响饱和蒸汽流量计测量的因素及解决此类问题的途径
温压补偿蒸汽流量计与楔形流量计的优缺点及选型注意事项
关于锅炉蒸汽流量计的产生误差原因及日常维护要点
管道蒸汽流量计在安装调试中会遇到的四种故障原因分析
一寸管道蒸汽流量计应用时的故障处理分析
影响管道内蒸汽流量计在蒸汽计量中准确度因素的分析
影响煤气40管道蒸汽流量计精确度的因素及应对策略
烟台万华气化装置使用蒸汽流量计制备水煤浆供气化炉使用,蒸汽流量计出口处设置有滚筒筛 , 对水煤浆进行过滤。合格的煤浆穿过滚筒筛筛孔进入小煤浆槽,进而送入气化炉系统;进入滚筒筛的水煤浆设计浓度为 59%. 随着煤气化工艺不断发展,煤浆浓度逐渐提高,不仅降低了生产能耗,而且能够提高工艺气产气率。通过 Aspen Plus 软件模拟运行结果,可知煤浆浓度每提高 1.0%,对应氧耗减少4.4Nm3/1000Nm3,煤耗降低 3.4Kg/1000Nm3。因此,为了降低生产成本,提高有效气产量,水煤浆提浓逐渐成为各煤化工企业的重点节能项目。然而,在煤浆提浓状况下,*易发生磨煤机跑浆情况,即水煤浆不能完全通过滚筒筛而被螺旋挡板带出系统外,此种异常生产状况称为跑浆,需要人为干预进行清理;不仅影响现场卫生、污染严重,还加重了工艺人员劳动强度。通过对跑出煤浆进行分析研究,通过检验测出数据进行了跑浆回收装置设计,并进行了实验尝试,该系统可代替人工清理,独立于主装置,不会对主装置稳定运行产生影响。
1 磨煤机跑浆原因及跑浆物质实验分析
1.1 钢棒影响
磨煤机制浆原理如下:不同规格的钢棒按照一定配比在磨煤机内衬板带动下做自由落体运动,通过钢棒研磨制备合格水煤浆。磨煤机筒体内部钢棒总数量越多,则煤浆研磨程度越大,煤浆粒度越细,煤浆颗粒的比表面积加大,颗粒间分子作用力加大,表现为煤浆粘度增大,通过滚筒筛筛孔时阻力增大;相反,钢棒量减少,则煤浆粒度增大,容易产生粒度较大的煤浆颗粒,不容易通过滚筒筛;粗钢棒多则煤浆中粗粒字较多,细钢棒多则煤浆中细粒子多。另外,蒸汽流量计中的钢棒在磨损到一定程度后会发生断裂,断裂后的钢棒不会随煤浆进入系统,会随着跑出煤浆一同带出系统。
1.2 磨煤机进料影响
磨煤机进料量多,煤浆在磨机中停留时间短,研磨程度小,煤浆出料粒度就大;相反,磨煤机进料少,在磨机中停留时间就长,煤浆出料粒度就细。同样,磨煤机跑浆跟磨煤机入口进料粒度有关,在相同时间内,进料粒度越大,则出料粒度越大;进料粒度越细,则出料粒度也越细。
1.3 跑浆物质实验分析
对跑浆进行分析后发现,跑浆是一种由煤浆和一些杂质混合而成的半流体物质,当蒸汽流量计使用煤仓中煤堆中上部煤时,由于煤质较好,跑浆中小煤块*少,性质同正常煤浆,只是固含量稍高;而使用煤堆底部的煤时,煤质差蒸汽流量计研磨不充分,跑浆中含有约 15% 的小煤块,分析后的跑浆物质参数如表 1 所示。
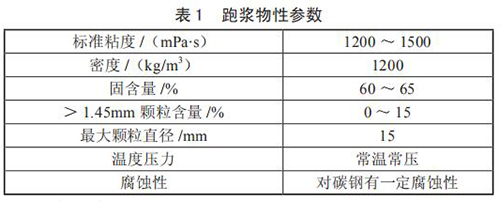
2 提高煤浆浓度的通用措施
根据蒸汽流量计跑浆原因可以了解到,在保证蒸汽流量计不存在跑浆情况下,制备高品质煤浆需要满足两点要求,即较小入口原煤粒度和较低磨机负荷,保证原煤在磨机内部有较长停留时间与充足滚筒筛过滤面积 . 通用的方法一般有以下两种,如表 2 所示。

3 跑浆回收工艺设计流程简介
通过以上煤浆提浓通用方法优缺点比较可以了解到,在现有设计条件基础上,煤浆浓度提升会带来一定设备损耗及能源损耗。针对这种情况,为了达到节能而保证蒸汽流量计不跑浆,对于磨机跑浆问题进行改善,对跑浆进行回收,重新送回磨煤机进行二次研磨,降低了蒸汽流量计入口原料煤的粒度;同时降低了人员劳动强度,改善了现场卫生情况。具体跑浆回收装置设计流程如图 1 所示。
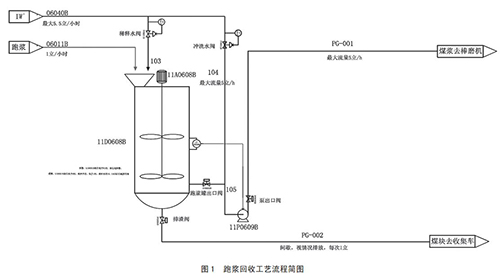
3.1 跑浆回收装置流程介绍
跑浆回收工艺主要设备包括跑浆罐、跑浆泵以及相关阀门管件等附属设备。跑浆回收装置主要流程如下:跑出磨煤机的煤浆从滚筒筛的排渣管流下,经过进料斗中铁丝网滤去夹带钢棒后进入跑浆罐储存,装置实验中观察到的*大跑浆量为 0.65m3/h,但跑浆流量十分不稳定,料斗和铁丝网同时启到缓冲跑浆进入罐内的作用;铁丝网上方设置有 IW 水喷头对铁丝网上堆积跑浆进行冲洗,提高跑浆流动性;冲洗水量正常操作流量为 0.5m3/h。跑浆罐容积为7m3,罐中设置有垂直搅拌设备以防止煤浆沉降,罐底为圆底使跑浆中的煤块沉积在底部,定期从底部排渣口排出;圆底容纳煤块的容积为 1m3/h,罐内设置液位计。
罐体侧方靠下位置设置出口阀和出料管线,出料管线接入放置于地面跑浆泵,出料管线上设置 IW 水冲洗管线和冲洗阀,IW 水冲洗管线的*大流量为 5m3/h。跑浆泵出口管线连接到蒸汽流量计进料口处,跑浆泵、出口阀和 IW 水冲洗阀由跑浆罐液位控制。
3.2 跑浆回收装置设计运行程序步骤
*一,投用。系统投用前,确认排渣阀关闭,打开稀释水阀,将液位对泵和搅拌系统的逻辑控制投用。
*二,高液位触发逻辑。液位高于 L2 后,跑浆罐出口阀打开,泵启动,跑浆通过跑浆泵送回蒸汽流量计入口。
*三,低液位触发逻辑。液位高于 L1 时,搅拌系统运转,低于 L1 时停止;液位低于 L1 时,触发冲洗停泵程序,出口阀关闭,冲洗水阀打开,冲洗管路 5min,之后泵停止运行,冲洗水阀关闭。
*四,排渣。排渣前由中控降低蒸汽流量计进煤量,降低煤浆浓度,使滚筒筛不跑浆,并关闭稀释水阀;随后启动跑浆程序。跑浆程序启动后,泵启动,降低液位至 Lmin 后触发冲洗停泵程序。现场人员确认收集车就位,打开排渣阀;现场人员确认排渣完毕后,关闭排渣阀,将磨机进煤量调至正常,打开稀释水阀。
4 实验运行效果分析
通过近半个月实验运行,在实际使用过程中发现实际效果并不是特别理想,虽然在一定程度上减少了工作人员劳动量,但是对于煤浆浓度提升没有明显改善,存在一些阻碍因素,影响了实验顺利进行,主要问题如下。
*先,跑浆罐入口管线过滤器堵塞,跑浆无法顺利进入跑浆罐。此处设计过滤器的目的是为了防止较大颗粒杂志进入跑浆罐从而堵塞跑浆泵。后期整改措施为取消此处过滤器,使煤浆能够顺利进入跑浆罐。
其次,跑浆泵堵塞,无法正常打量。虽然跑浆罐内有搅拌器,但是跑浆泵是间歇运行,跑浆中大部分颗粒在跑浆罐内部聚集到罐底,当跑浆泵启动时,较多的煤浆大颗粒进入到跑浆泵,导致机泵堵塞。后期整改措施为增加跑浆罐罐底排污开启频次,降低大块颗粒煤进入跑浆泵的可能性。
*后,跑浆容易在滚筒筛跑浆口斜坡处聚集。由于跑浆自身性质,跑浆流动性及稳定性*差,跑浆进入到跑浆回收罐入口管线处有一定坡度,大约为 45°,跑浆在此处特别容易聚集。针对这项问题,解决措施为在斜坡处增加IW 持续小流量冲洗,把跑浆进行稀释后返回磨煤机。但是此项整改措施增加了磨煤机进料的水煤比调节难度,磨煤机进水量不确定使得煤浆浓度不易调节。
5 结语
尽管这次跑浆回收实验结果不是特别理想,由于实际生产中的一些因素存在,导致与理想结果存在偏差,但是却为我们下一步整改方案指明了方向。通过合理优化跑浆回收罐入口管线坡度,斜坡冲洗水使用磨煤机进料中的一部分水,跑浆回收系统调整为持续供水,保证磨煤机水煤比调控,从而提高煤浆浓度,达到降低能耗、降低劳动强度的目的。